Unlocking Efficiency and Precision: A Deep Dive into Standing Seam Metal Roof Roll Formers
- Share
- Issue Time
- Jul 14,2025
Summary
This comprehensive guide explores the world of standing seam metal roof roll formers. Discover the significant advantages of portable on-site roll forming, including reduced costs, waste, and logistical challenges. We'll compare portable versus in-plant machines, delve into the crucial factors for choosing the right machine for your business, identify top manufacturers in the industry, and provide essential maintenance tips to ensure the longevity and performance of your investment. This article
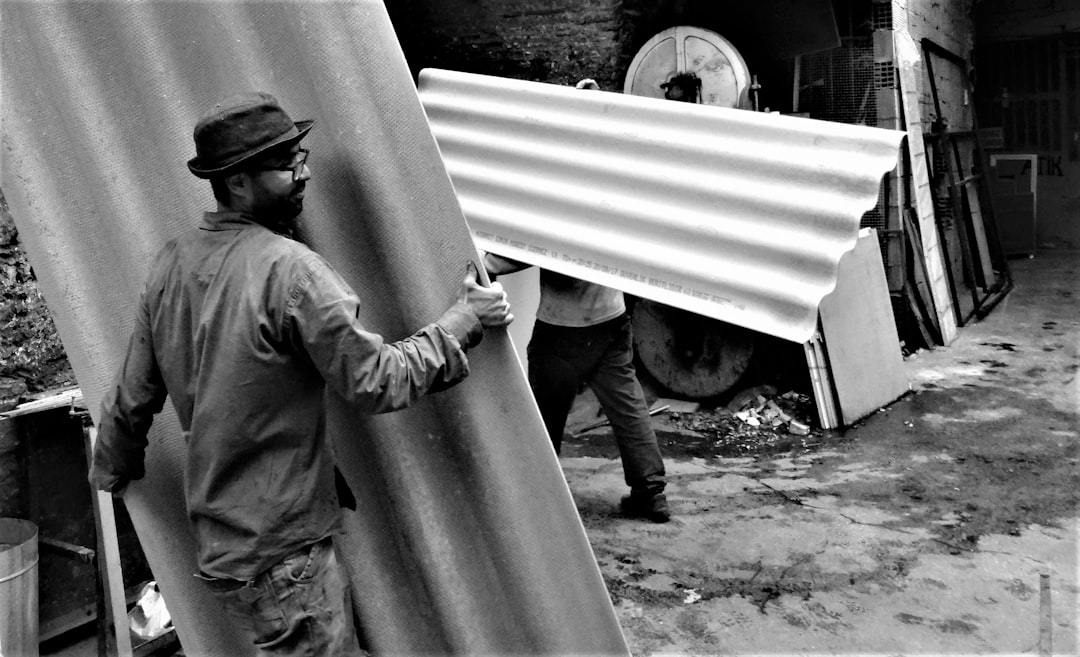
Standing seam metal roofing has become a hallmark of modern construction, prized for its durability, longevity, and sleek aesthetic. At the heart of this industry are standing seam metal roof roll formers, the machines that fabricate the panels with precision and efficiency. Whether you're a seasoned contractor or new to the metal roofing business, understanding this technology is crucial for success. These machines transform coils of metal into high-quality, weather-tight roofing panels, offering a significant advantage over pre-fabricated options.
The Power of Portability: On-Site Roll Forming Advantages
The most significant industry shift has been toward portable roll forming. Bringing the factory directly to the job site offers numerous benefits that boost efficiency and profitability.
- Eliminate Shipping Constraints and Damage: One of the biggest challenges with factory-formed panels is their length limitation for transportation. Portable roll formers allow you to create continuous panels of virtually any length directly on-site, from the eave to the ridge. This eliminates the need for panel laps, which are potential points of failure, resulting in a more weather-tight roof. It also completely removes the risk of panels being damaged during transit.
- Reduce Costs and Waste: By forming panels to the exact required length, waste is significantly minimized compared to cutting down longer, pre-manufactured panels. Furthermore, you save a substantial amount on shipping and packaging costs, especially for large projects or long panels. Contractors purchase metal as coil, which is more cost-effective than buying finished panels, and those savings can be passed on to the customer.
- Increase Flexibility and Speed: On-site forming means no more waiting for panel deliveries. Production is fast, with some machines capable of producing up to 150 feet per minute, allowing installation crews to work continuously without costly delays. This just-in-time production model gives contractors ultimate control over their project schedules.
Choosing Your Machine: Portable vs. In-Plant Roll Formers
The decision between a portable and a stationary in-plant roll former depends largely on your business model.
Portable Roll Formers are the versatile choice for small to medium-sized contractors. They offer the flexibility to work on-site or in your shop. While their production speed is slower than their in-plant counterparts, it's more than sufficient for most residential and commercial projects. The ability to offer multiple profiles from a single machine adds to their value.
In-Plant Roll Formers are industrial workhorses designed for high-volume, continuous production. They are faster, can handle larger coils, and are built for non-stop use, making them ideal for large-scale manufacturers supplying panels in bulk. However, this power comes with a significantly higher price tag, starting at around $400,000, and requires substantial facility space.
For many, a hybrid approach works best, using portable machines in-house for smaller runs and on-site for custom jobs, providing the best of both worlds.
Key Factors in Selecting a Standing Seam Roll Former
Investing in a roll former is a significant decision. Consider these factors carefully to ensure you choose the right machine for your business needs:
- Panel Profiles: What types of panels do you plan to offer? Machines can be tooled for various profiles like snap-lock, mechanical seam, and fastener flange. Multi-profile machines offer the greatest versatility, allowing you to change tooling to produce different panel styles.
- Production Capacity & Materials: Assess your required output volume. Also, ensure the machine can handle the types of material (steel, aluminum, copper) and gauges you intend to use.
- Budget and ROI: Prices for portable machines vary widely, from around $37,000 for an entry-level model to over $164,000 for a fully-equipped, multi-profile machine with a trailer. Analyze the total cost of ownership, including accessories and maintenance, and weigh it against the potential return on investment from increased efficiency and reduced material costs.
- Manufacturer and Support: Choose a reputable manufacturer known for quality and reliability. Leading names in the industry include New Tech Machinery, The Bradbury Group, Englert Inc., and Roll Former Corporation. Look for companies that offer comprehensive training, technical support, and readily available parts.
Top-Tier Standing Seam Roll Former Manufacturers
The market for roll forming machines is competitive, with several key players known for their quality and innovation.
- New Tech Machinery (NTM): A leading manufacturer of portable roll formers, NTM is known for versatile machines like the SSQ II™ MultiPro, which can produce numerous roof and wall panel profiles.
- The Bradbury Group: A global leader in both in-plant and portable equipment, Bradbury machines are recognized for their high quality, integrated technology, and high production speeds.
- Englert Inc.: Englert offers a complete package with their "MetalMan" machines, providing the machine, coil, training, and support for an all-in-one solution.
- Roll Former Corp: Specializing in a wide variety of machines, Roll Former offers robust and reliable portable options for on-site fabrication.
- Schlebach Maschinen GmbH: A German manufacturer with a global presence, Schlebach offers a diverse range of high-quality profiling and seaming machines.
Essential Maintenance for Longevity and Performance
Proper maintenance is not a chore; it's insurance for your investment. A well-cared-for machine will deliver consistent, high-quality panels and prevent costly downtime.
- Daily/Weekly Checks: Before starting a job, always inspect the machine. Keep the drive and forming rollers clean from debris and metal shavings to avoid marking the panels. Ensure chains are properly lubricated and check for any loose hardware.
- Lubrication: Regularly lubricate all moving parts, including chains, gears, and the shear blade, according to the manufacturer's schedule.
- Proper Storage: Protect your machine from the elements. Whenever possible, store it indoors or in a well-ventilated trailer to prevent condensation and rust. Never transport the machine with material threaded through it.
A disciplined maintenance program protects your machine, your schedule, and your reputation, ensuring you can continue to produce top-quality standing seam metal roofs for years to come.