The Ultimate Guide to Roofing Sheet Roll Forming Machines: Boosting Efficiency and Quality in 2025
- Share
- Issue Time
- Jul 13,2025
Summary
A deep dive into roofing sheet roll forming machines, the cornerstone of modern metal roofing production. This guide explores how these machines operate, their core benefits, the different types available, and key factors to consider before investing. Discover how this technology increases productivity, ensures precision, and provides a significant competitive edge in the construction industry by transforming raw metal coils into durable, high-quality roofing panels. [1, 3, 4, 30]
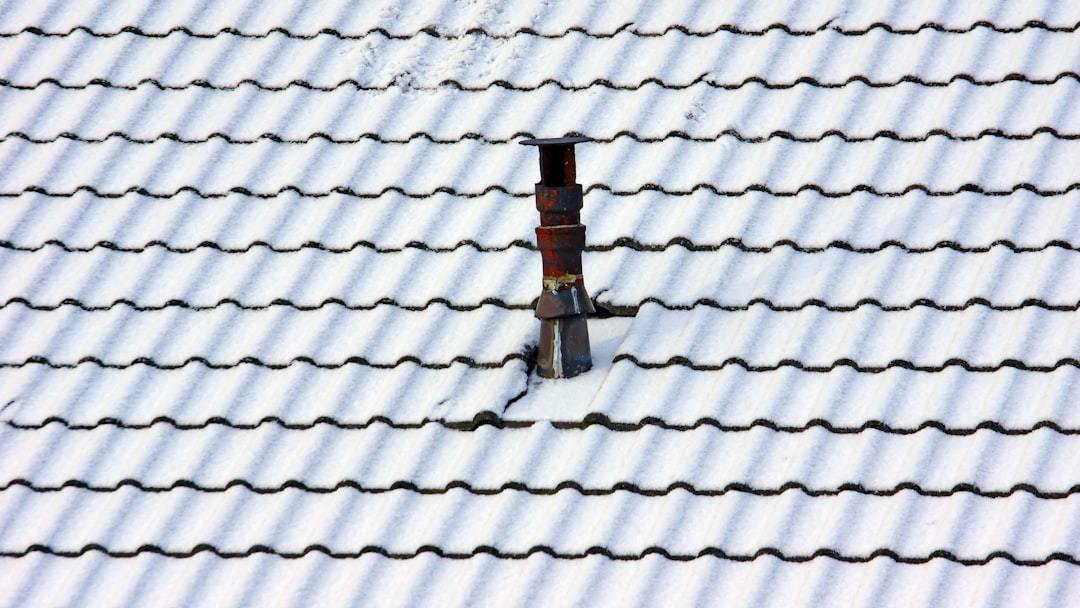
In today's fast-paced construction industry, efficiency, precision, and cost-effectiveness are paramount. The roofing sheet roll forming machine stands at the forefront of this evolution, revolutionizing how metal roofing panels are produced. This essential piece of equipment transforms flat metal coils into a variety of durable and aesthetically pleasing roofing profiles, making it a vital asset for manufacturers and large-scale roofing contractors. By automating the production process, these machines significantly boost productivity, reduce labor costs, and minimize material waste.
What is a Roofing Sheet Roll Forming Machine?
A roofing sheet roll forming machine is a specialized piece of industrial equipment designed to continuously bend and shape a long strip of sheet metal into a specific, desired cross-sectional profile. Unlike press braking or stamping, which are intermittent processes, roll forming is a continuous operation that makes it ideal for producing long runs of roofing panels with exceptional consistency and speed. These machines are the backbone of producing everything from common corrugated sheets to complex standing seam panels for residential, commercial, and industrial applications.
How Does the Roll Forming Process Work Step-by-Step?
The principle behind a roll forming machine is elegantly simple yet highly effective. The entire process is a seamless, automated flow from raw material to finished product.
- Decoiling/Uncoiling: The process starts with a large coil of metal (often galvanized steel or aluminum) being loaded onto an uncoiler, which carefully feeds the flat sheet into the machine.
- Guiding and Leveling: The sheet passes through an entry guide and leveling rollers to ensure it is perfectly flat and aligned before it enters the forming stage. This step is crucial for eliminating imperfections.
- Roll Forming Stations: This is the core of the machine. The metal strip moves through a series of stations, each equipped with a set of precisely crafted rollers. Each station performs a small, incremental part of the bending process, gradually shaping the metal into the final profile.
- Cutting System: Once the profile is formed, it moves to an automated cutting station. A hydraulic or mechanical shear cuts the continuous sheet into pre-programmed, precise lengths without halting the production line.
- Output and Stacking: The finished, cut-to-length roofing sheets are then conveyed to an exit table or an automatic stacker, ready for packaging and transport.
Exploring the Different Types of Roofing Sheet Machines
Roll forming machines are versatile and can be designed to produce a wide array of roofing profiles. The type of machine you need depends entirely on the end-product desired.
- Corrugated & Trapezoidal (IBR) Machines: These are the most common types, producing the classic wavy (corrugated) or box-rib (trapezoidal/IBR) panels. These profiles are valued for their strength and are widely used in industrial and agricultural buildings.
- Tile Effect / Glazed Tile Machines: These advanced machines create profiles that mimic the look of traditional ceramic or glazed roof tiles. They offer the aesthetic of classic tiles with the durability and light weight of metal, making them popular for residential properties.
- Standing Seam Machines: Produce panels with raised, interlocking seams that conceal fasteners, providing a sleek, modern look and superior weather resistance. They are a premium choice for architectural and high-end commercial roofing.
- Double Layer / Dual Level Machines: A highly efficient design where two different roll forming lines are stacked vertically. This allows a manufacturer to produce two different profiles (e.g., an IBR panel and a corrugated panel) with a single machine, saving valuable floor space and budget.
- Portable Roll Formers: Compact machines designed to be taken directly to a job site. This offers incredible flexibility, reduces shipping costs and damage, and allows for the creation of custom-length panels on-site, which drastically minimizes waste.
The Key Benefits of Investing in a Roll Forming Machine
Investing in a roll forming machine offers substantial advantages that can give a business a significant competitive edge in the market.
- Increased Productivity and Speed: These machines are built for high-volume output, with some capable of producing panels at speeds of over 25 meters per minute, drastically shortening project lead times.
- Cost-Effectiveness: While the initial investment is significant, the long-term savings are substantial. Automation reduces labor requirements, and the precision of the process minimizes material scrap and waste.
- Unmatched Precision and Consistency: The roll forming process ensures every panel produced is identical, guaranteeing high-quality, uniform products that meet strict industry standards.
- Flexibility and Customization: Modern machines, often equipped with PLC control systems, can be easily programmed to produce different lengths and quantities, offering great operational flexibility.
How to Choose the Right Roofing Roll Former for Your Business
Selecting the right machine is a critical decision that depends on your specific business needs. Here are key factors to consider:
- Production Needs: Evaluate your required production speed and volume. A smaller operation may not need the high-speed capabilities of a top-tier machine.
- Material Compatibility: Ensure the machine can handle the type (steel, aluminum) and thickness of the metal you plan to use.
- Profile Requirements: Determine which roofing profiles are in demand in your market. A versatile double-layer machine might offer a better return on investment than a single-profile machine.
- Automation Level: Consider the level of automation you need. Fully automated lines with auto-stackers increase efficiency but also cost more.
- Manufacturer Reputation and Support: Choose a reputable manufacturer that provides a solid warranty, technical training, and reliable after-sales service.
Essential Maintenance and Operational Tips
To ensure the longevity and peak performance of your roll forming machine, a regular maintenance schedule is crucial.
- Regular Lubrication: Keep all gears, chains, and bearings properly lubricated according to the manufacturer's schedule to prevent premature wear.
- Keep Rollers Clean: Regularly wipe down the forming rollers to prevent debris from marking or damaging the finished panels.
- Check Hydraulic Fluid: For machines with hydraulic cutters, monitor the hydraulic oil level and quality, changing it as recommended.
- Inspect Tooling and Alignment: Periodically check the alignment and gaps of the roll tooling to ensure product quality and prevent damage to the machine.