The Ultimate Guide to Aluminum Roll Forming Machines: Efficiency, Precision, and Applications
- Share
- Issue Time
- Jul 11,2025
Summary
Discover the essential guide to aluminum roll forming machines. This article explores the intricate process of how these machines work, their key components, and the significant advantages they offer over other metal forming techniques. We delve into their diverse applications across industries like automotive and construction, highlighting how they produce lightweight, durable, and complex profiles with high precision and efficiency. Whether you're a manufacturer or an engineer, understand why
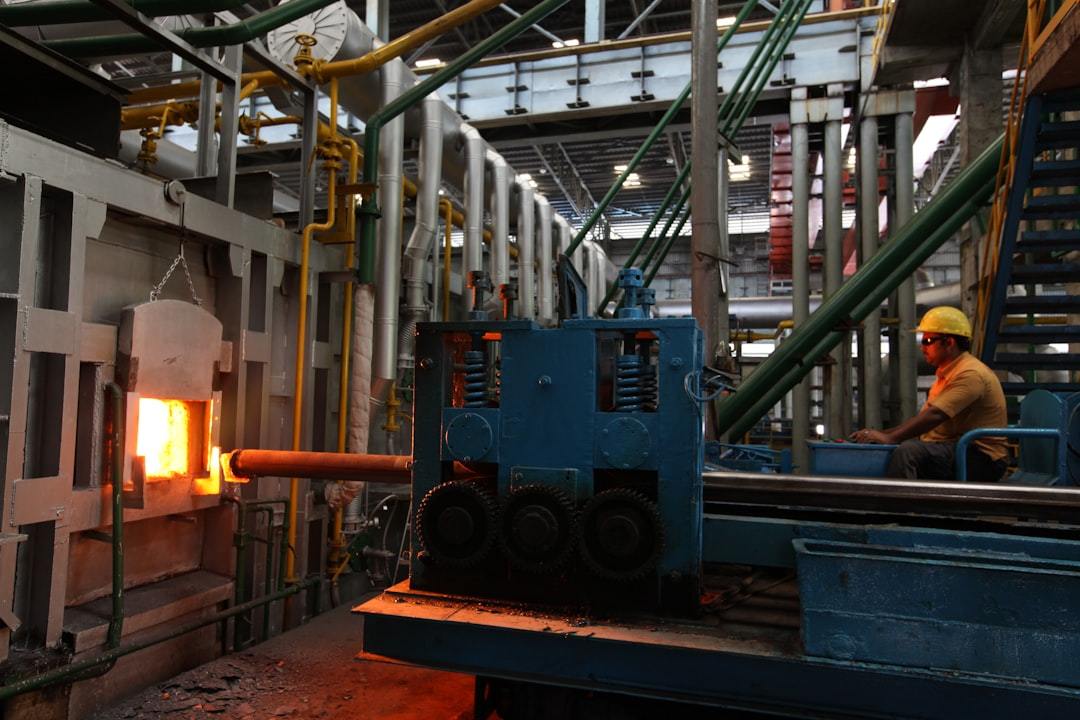
Aluminum roll forming is a pivotal technology in modern manufacturing, enabling the creation of uniform, complex, and high-strength metal components at scale. By progressively shaping a continuous strip of aluminum through a series of rollers, this process delivers precision and efficiency that other methods struggle to match. From the robust frames of vehicles to intricate construction profiles, aluminum roll forming machines are the engines driving innovation and productivity across numerous sectors.
How Does the Aluminum Roll Forming Process Work?
The aluminum roll forming process is a marvel of continuous, automated manufacturing. It begins with a large coil of aluminum sheet, which is loaded onto a decoiler. The strip is then fed through a straightener to ensure it is perfectly flat before it enters the forming stages.
The core of the machine consists of multiple sets of roller stations. As the aluminum strip passes through each station, pairs of rollers progressively bend and shape the metal. Each station contributes a small part of the final profile, ensuring minimal stress on the material and preventing defects like cracking or tearing. This incremental approach allows for the creation of highly complex cross-sections with extreme precision and consistency. After the profile is formed, it is cut to the desired length by an integrated cutting system, such as a flying shear, without halting the production line.
Key Components of a Roll Forming Machine
Understanding a roll forming machine requires knowing its essential components, which work in unison to transform a simple metal coil into a finished product. While designs vary, most machines include the following key parts:
- Decoiler: This holds the master coil of aluminum and feeds it into the line in a controlled manner.
- Entry Guide/Straightener: Aligns and flattens the metal strip to prepare it for forming.
- Rolling Stations: These are the heart of the machine, comprising a series of rollers (or roll stands) that gradually shape the metal.
- Drive System: A powerful motor and a series of gears that drive the rollers and pull the material through the machine.
- Cutoff Press/Shear: An automated system that cuts the formed profile to a specific length with high accuracy.
- Control System (PLC): The brain of the operation, this system controls the machine's speed, cutting, and other parameters, ensuring precision and automation.
The Unmatched Advantages of Aluminum Roll Forming
Manufacturers increasingly choose roll forming for aluminum due to its significant advantages over processes like press braking or extrusion. The benefits are clear and impactful:
- High Efficiency and Speed: Roll forming is a continuous process ideal for high-volume production, with some machines forming metal at speeds of 30 to 100 feet per minute.
- Consistency and Precision: The process produces highly uniform parts with tight tolerances, which is crucial for components used in assembly. This repeatability minimizes issues in the final product assembly.
- Material Versatility and Strength: Aluminum is an ideal material for roll forming. It's lightweight, naturally corrosion-resistant, and boasts an excellent strength-to-weight ratio. Some aluminum alloys can be stronger than steel.
- Design Flexibility: The process allows for the creation of complex and intricate profiles. In-line processes like punching, notching, and embossing can be integrated, reducing the need for secondary operations and lowering costs.
- Cost-Effectiveness: For high-volume projects, roll forming is exceptionally cost-effective due to high production speeds, reduced labor costs, and minimal material waste.
Wide-Ranging Applications Across Industries
The versatility of aluminum roll forming makes it indispensable in a vast array of industries. In the construction sector, it is used to produce roofing panels, gutters, downspouts, window frames, and structural components. These materials are valued for being sturdy, lightweight, and easy to install.
In the automotive and transportation industry, roll forming is essential for manufacturing lightweight yet strong parts such as bumpers, chassis components, and trim. The use of aluminum helps reduce vehicle weight, which improves fuel efficiency and lowers emissions. Other significant applications include enclosures and heat sinks for the electronics industry, frames for solar panels, and components for furniture and appliances.
The Future of Aluminum Roll Forming
The future of aluminum roll forming is bright, driven by increasing demand for lightweight and sustainable materials. As industries like automotive and aerospace continue to prioritize weight reduction to enhance efficiency and performance, the role of aluminum will only grow. Machine technology is also advancing, with better automation and the ability to handle higher-strength aluminum alloys. This ongoing innovation ensures that aluminum roll forming machines will remain a cornerstone of efficient, high-quality manufacturing for years to come.