Roll Forming Aluminum: A Comprehensive Guide to Processes, Benefits, and Applications
- Share
- Issue Time
- Jul 17,2025
Summary
Discover the efficiency and versatility of roll forming aluminum. This guide explores the complete process, its key advantages like strength, consistency, and cost-effectiveness, and its wide-ranging applications in industries from automotive to construction. Learn why this cold forming technique is a premier choice for creating high-quality, durable, and complex metal profiles.
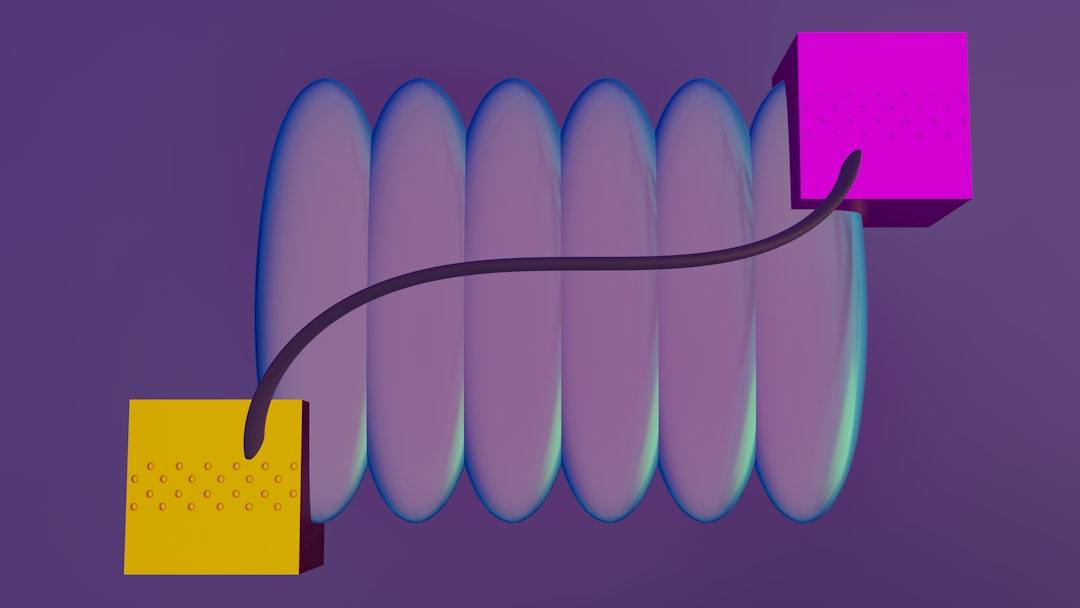
In modern manufacturing, efficiency, precision, and versatility are paramount. Roll forming aluminum stands out as a superior fabrication process that meets these demands, transforming coils of sheet aluminum into high-strength, complex profiles with remarkable consistency. This continuous and highly efficient process is essential for numerous industries, delivering parts that are both lightweight and durable.
What Exactly is Aluminum Roll Forming?
Roll forming is a continuous bending operation where a long strip of aluminum sheet, typically fed from a coil, is passed through a series of rollers. Each set of rollers progressively shapes the metal, incrementally bending it until the desired cross-sectional profile is achieved. Unlike other processes, roll forming is a cold forming method, meaning it's performed at room temperature without the need for heat. This not only saves energy but also enhances the material's strength through work hardening. The result is a perfectly uniform part, ideal for producing long lengths and high volumes of components.
The Step-by-Step Roll Forming Process
While seemingly complex, the roll forming process can be broken down into several distinct stages, all seamlessly integrated into a single production line to maximize efficiency:
- Uncoiling: A large coil of aluminum sheet metal is placed on an uncoiler, which allows the material to be fed into the machine smoothly.
- Infeed and Leveling: The strip is fed into the machine and often passes through a leveling station to ensure it is perfectly flat before forming begins.
- Progressive Forming: This is the core of the process. The aluminum sheet travels through a series of specially designed roll stations. Each station has a pair of rollers that precisely bend a small portion of the profile. With each successive station, the shape becomes more defined.
- In-line Processing (Optional): One of the major advantages of roll forming is the ability to incorporate other manufacturing processes in-line. This can include punching holes, adding notches, embossing, or cutting the profile to specific lengths.
- Cut-off and Discharge: Once the profile is fully formed, a high-speed cutting press cuts it to the predetermined length without stopping the line. The finished parts are then discharged for stacking and shipping.
Key Benefits of Choosing Roll Formed Aluminum
The advantages of roll forming aluminum make it a preferred choice for a wide array of applications:
- High Efficiency and Speed: As a continuous process, roll forming is incredibly fast and efficient, making it ideal for high-volume production runs.
- Consistency and Precision: The process produces parts with uniform thickness, extremely tight tolerances, and consistent shapes from the first piece to the last.
- Enhanced Strength: Although aluminum is naturally lightweight, the cold working process of roll forming increases its tensile strength, resulting in a stronger, more durable final product.
- Cost-Effectiveness: For large projects, roll forming is highly cost-efficient due to high production speeds, lower labor costs, and minimal material waste.
- Design Flexibility: The technique allows for the creation of complex shapes and profiles, including round, closed, and C-shaped cross-sections, giving designers significant creative freedom.
- Superior Finish: Roll forming creates a uniform and consistent finish, which is often desirable for parts that are visible in the final product, such as decorative trims or panels.
Common Applications Across Industries
The unique combination of lightness, strength, and corrosion resistance makes roll formed aluminum a vital component in many sectors.
- Construction: Widely used for roofing, wall panels, framing, window frames, and gutters. Its durability and resistance to atmospheric agents are critical in this field.
- Automotive: Essential for manufacturing lightweight yet strong components like bumpers, door frames, and chassis components, which helps improve fuel efficiency.
- Renewable Energy: Used to construct support systems for solar panels and components for wind turbines where durability is paramount.
- Furniture and Design: Designers use rolled profiles for decorative elements and structural parts, taking advantage of the fine finishes and complex shapes possible.
- Industrial and Retail: Components for racking systems, conveyor belts, and tracks in automated fulfillment centers are often made through aluminum roll forming.
Roll Forming vs. Aluminum Extrusion
While both are popular methods for shaping aluminum, they are fundamentally different. Extrusion involves pushing a heated aluminum billet through a die to create a shape, much like squeezing toothpaste from a tube.
Roll forming is generally faster and more cost-effective for high-volume production of long, uniform parts. Extrusion, however, excels at creating more intricate and complex cross-sections, including hollow profiles, and can offer better tensile strength, especially after heat treatment. The choice between the two often comes down to the project's specific requirements, including profile complexity, production volume, and material thickness.
Ultimately, aluminum roll forming is a sophisticated and highly advantageous manufacturing process. Its ability to produce consistent, strong, and cost-effective components makes it an indispensable technology for engineers and product designers looking to innovate and build for the future.